Introduction
You’ve just heard from DACTEC that your new chamber is going to be delivered soon, so what are the most important steps you need to take in order to start using it as soon as possible after it arrives? What are the installation requirements for your new chamber?
You may have decided already where to site your new chamber but have you taken into account the finer details that could affect the optimal running of the chamber? What utilities will be needed?
These are the questions that need to be considered before the chamber arrives on site.
Before we get started, here is one question which should be considered even before you purchase the chamber. What is the access route to the chamber’s final location? Take into consideration door sizes, stairs or lift access, turning points etc.
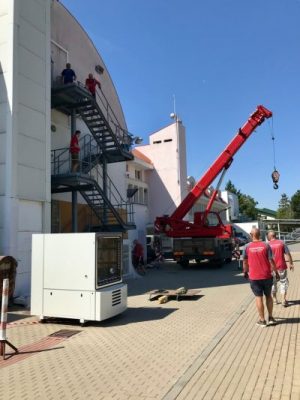
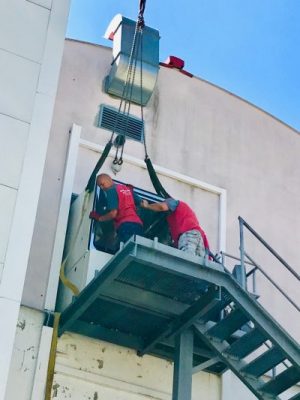
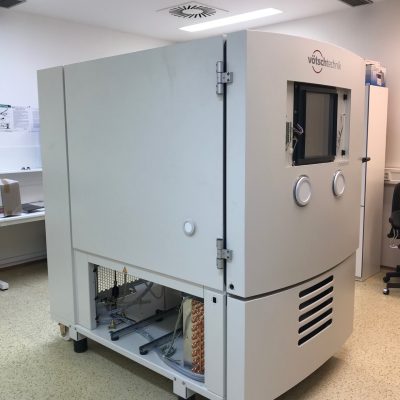
Where to site your chamber
The chamber should be on a level surface out of direct sunlight and away from sources of heat and extreme humidity.
There should be space around the chamber to facilitate service, that distance will be specified in the quote documents e.g. 700mm. If you’ve bought a chamber with wheels it can be pushed in closer to the walls if the power cable, water and drain piping are flexible and long enough. Wheels are an optional extra on Weiss chambers. However, this space saving option is not possible if the chamber is plumbed up to an external condenser.
If there is an internal condenser the heat taken from the test space is emitted into the room. Your air conditioning needs to be able to handle that because if the room gets too hot, cooling power will drop off and the chamber will stop with an error.
If you site the chamber in an office area, bear in mind that even the quietest chamber emits noise.
When the chamber arrives, you should be prepared to unload it, unpack it, transport it to its final location and connect all services.
Utilities
Power
If the chambers require single phase mains voltage, only the smallest can use a domestic plug top and otherwise an electrician can supply a more powerful outlet. It is recommended that all outlets have an on/off switch and an ELCB on this outlet.
Most chambers require a 3-phase supply and this should also have an on/off switch and an ELCB on this outlet.
The current rating will be detailed in your quote documents.
Drain
Any chamber can produce condensation, so a drain is required. For some chambers and applications, a collection vessel is sufficient but this must be monitored regularly and emptied before it overflows and causes a slip hazard. It is therefore better to attach the chamber’s condensate outlet to a proper drain.
If your drain is located elsewhere a condensate pump can be used to transport the water from the condensate outlet to your drain. Recycling the condensate back into the reservoir is not recommended as a build-up of contaminants can occur.
Water for humidity control
You can manually fill your chamber’s reservoir but it could run low during a long test. Alternatively, you can attach the chamber to a constant supply. In that case a drain is required in case of overflows.
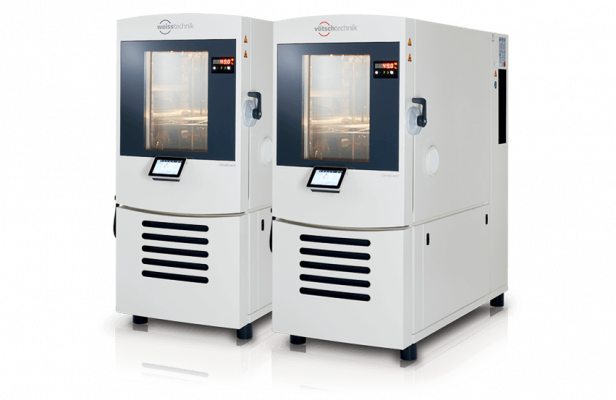
If your water supply contains excess salts they will gather in the humidifier and can also condense as a fine powder in the chamber test space. On the other hand, if the water is too pure it will act like an ‘ion magnet’ stripping ions from its surroundings and can become aggressive.
The specification is between 5 and 20uS/cm, PH 6 to 7, pressure 1.5 to 6 bar. If you do not have that supply in your premises, DACTEC can supply an ion exchange filter that can bring municipal tap water to the required specification. One of these filters can supply several chambers simultaneously.
Water for cooling
Weiss & Votsch faster stress chambers come as standard with a cooling water inlet and outlet for connection to a site chilled water system. If you do not have one of these we can supply and install an external air-cooled condenser but they reduce the cooling power by approximately 5%.
The main requirements for cooling water are 2.5 to 6 bar inlet and the outlet back pressure must be 2 bar lower. This difference is what causes customers most trouble after instillation and it is a good idea to stress the importance of this to your Facilities Department in good time to avoid issues.
The outlet back pressure is not a function of the chamber but is a function of the length and diameter of the return piping amongst other things. Because of this DACTEC would insist on pressure gauges being installed at the cooling water inlet and outlet of the chamber by the customer.
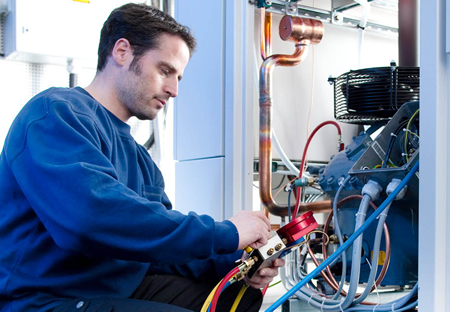
The temperature of the water supply must be between 12 and 28°C. Running outside these specs can damage your chamber. The PH should be around 7 and there should be no contaminants grater than 100 micrometres.
Compressed air or nitrogen
Some Weiss & Votsch chambers are purchased with options that require compressed air e.g. low dew point control or nitrogen to prevent oxidation. Consult your quote to see what you must supply and connect e.g. pressure 6 to 12 bar. If you have a compressed air supply with a low dew point you may not need a built-in dryer in the chamber. In this case the dew point of your air supply should be lower than the dew point you require to test at.
External communications
Weiss chambers can be controlled in different ways: Weiss Simpati software, ASCII commands, Labview or Weiss Simserve. Also, you can control your chamber over the internet as standard without the need for special software. The chamber can also be configured with analog outputs for data recording. A CSV data file can be recorded to a USB stick as standard on most Weiss chambers.
Pharma customers may need independent monitoring. This can be done with a built-in probe or a remote probe connected to your BMS/LIMS system. These options can be discussed with DACTEC.
More Information
We hope that the information in our blog ‘Installation Requirements For Your New Chamber’ has been helpful and that when your new chamber arrives, by using these guidelines, it will be up and running your tests quickly and with optimal operation performance.
You might also find the following blogs of interest:
- Maintaining Your Chamber
- Why Our Customers Value Local-service
- 15 Reasons Customers Chose DACTEC Ltd to Service Their Chambers
If you would like more information about DACTEC’s service support, such as:
- Service Agreements
- IQOQ, IPV’s, Calibration and Validation
- Spare Parts and Consumables
- Installations
- Call-Outs
- Maintaining Your Chamber
Please click here.
See what our customers say about DACTEC on our Testimonial page.
For a full description of our offerings and a quote please contact us.